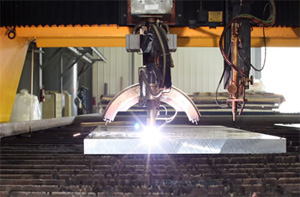
The services of plate cutting companies cannot take place without the machines that make the cutting task possible. These machines usually include:
-
Welding devices
-
Plasma cutters
-
Laser cutters
-
Waterjet cutters
The more popular forms used by the majority of plate cutting companies are plasma cutters, and waterjet cutters.
Both the plasma systems and waterjet systems have many advantages and come in alternative forms to better match the needs of each specific cutting styles and operators. Portable, stationary, manual, and automatic machines are all available in both plasma systems and waterjet systems. Each of these types can be further divided, as plasma cutters and waterjet cutters come in even more specific models like plasma gouging, oxyfuel gouging, and abrasive waterjet systems, just to name a few.
To decided which method is most appropriate, the type of material that requires processing must be considered. It is also helpful to consider the density of the material, the type of cut required, the level of accuracy needed, the rate of production, and the cost to operate.
Plasma systems are currently the most appropriate machines for cutting alloy based materials. While waterjet systems work well with metals, plasma models are known to produce better results when working with metal. Additionally, waterjet cutting machines cannot cut all grades of steel.
Waterjet cutting systems work well with a variety of materials, in addition to metal. For instance, when cutting softer materials like foam, rubber, plastic, and even paper, waterjet cutting machines are the best choice.
In plasma cutters, an inert gas like nitrogen, argon, oxygen, or hydrogen, is used to create a beam of plasma that cuts the workpiece.
The gas is under extreme pressure, while also flowing at speeds of approximately 20,000 feet per second. As it flows down a narrow path within the plasma head, it passes a negatively charged electrode. When the plasma nozzle touches the workpiece, this electrode is powered, causing an electric arc. Thus, the gas changes to plasma due to the high temperatures.
The beam in plasma cutters can reach temperatures of up to 30,000 degrees Celsius. To manage the direction and radius of the beam, plasma cutting devices employ what is called shielding gas.
A downfall of plasma cutters are heat affected zones. Heat affected zones, or HAZ's refer to the areas of the workpiece where the integral structure has been compromised. In turn, the durability of the material decreases, impacting the structures it helps to construct, such as bridges, skyscrapers, and air crafts.
Regardless of the model, no waterjet cutting machine produces HAZ's as it does not rely on heat to cut materials.
Waterjet cutting machines utilize an extremely fast flowing jet of water that is compressed under pressures of about 90,000 pounds per square inch. Machines using this particular process are called pure waterjet cutters. To cut tougher materials like titanium, granite, and wood, abrasive waterjet systems are used.
Abrasive waterjet cutters follow the same process as pure waterjes however, rather than using plain water as the cutting solution, a mixture of water and an abrasive like garnet, and aluminum oxide is used.
As mentioned, one of the benefits of using waterjet systems is the ability to produce no HAZ's. It can also cut a massive variety of materials, and is considered a "green” technology since the water in both pure and abrasive models can be recycled. However, in regard to efficiency, plasma cutting systems are far better at working with metals. Additionally, while waterjet machines and plasma machines are both affordable, the abrasives used in abrasive waterjet solutions can be quite costly to replace.
Plasma cutting systems and waterjet cutters are both frequently used within the precision cutting industry. Each have an assortment of advantages and produce great results. One of the main deciding factors for companies employing either system is the type of material of the workpiece. For alloy oriented materials, plasma cutters are usually operated as they work better with metal when compared to waterjet systems.